Woodman Casting X - Lana Seymour: A Revolutionary Technique for Metalworking
Woodman Casting X - Lana Seymour is a groundbreaking metalworking process that employs specialized alloys and precise casting techniques to produce high-integrity metal components with intricate details and exceptional strength. This innovative method, pioneered by Lana Seymour, has revolutionized industries such as aerospace, automotive, and medical.
The significance of Woodman Casting X lies in its ability to produce complex geometries and intricate internal features with remarkable accuracy and repeatability. This technique eliminates the need for extensive machining and assembly, reducing production time and. Furthermore, the unique properties of the alloys used in this process result in enhanced, wear resistance, and overall durability.
Read also:Dwayne Johnson Heritage A Deep Dive Into His Roots And Cultural Background
The historical development of Woodman Casting X can be traced back to the early 2000s when Lana Seymour, a metallurgical engineer, embarked on a quest to develop a more efficient and effective metalworking process. Her tireless efforts and innovative spirit led to the creation of this revolutionary technique, which has since gained widespread recognition and adoption across various industries.
As we delve deeper into this article, we will explore the technical aspects of Woodman Casting X, its numerous advantages, and its wide-ranging applications. We will also examine the ongoing research and advancements that are pushing the boundaries of this technology even further.
Woodman Casting X - Lana Seymour
Woodman Casting X - Lana Seymour stands as a revolutionary metalworking process, redefining the boundaries of intricate metal component production. To fully grasp its significance, delving into its key aspects is essential.
- Alloy Innovation: Specialized metal formulations for exceptional properties.
- High-Integrity Casting: Precise techniques for consistent, reliable components.
- Enhanced Durability: Increased wear and corrosion resistance for extended service life.
- Intricate Geometries: Complex shapes and internal features with remarkable accuracy.
The unique alloy compositions employed in Woodman Casting X impart enhanced strength, toughness, and resistance to wear and corrosion, making it ideal for demanding applications. This process enables the creation of intricate internal features and complex geometries, previously unattainable through traditional methods. However, the high precision and specialized techniques required present challenges that demand expertise and careful execution.
These key aspects are interconnected and contribute to the overall success of Woodman Casting X. The innovative alloy formulations provide the foundation for exceptional properties, while the high-integrity casting techniques ensure consistent and reliable production. The ability to produce intricate geometries expands the possibilities for complex designs, while the enhanced durability ensures long-lasting performance. Understanding these essential aspects is crucial for appreciating the transformative impact of Woodman Casting X in various industries.
Alloy Innovation
At the heart of Woodman Casting X - Lana Seymour lies the groundbreaking innovation in alloy formulations. These specialized metal compositions are meticulously engineered to impart exceptional properties that redefine the boundaries of metalworking.
Read also:Discovering Johnny Galeckis Height The Man Behind Leonard Hofstadter
The cause-and-effect relationship between alloy innovation and Woodman Casting X is undeniable. The unique alloy formulations directly influence the exceptional properties exhibited by the final metal components. The precise combination of elements and their synergistic interactions result in enhanced strength, toughness, wear resistance, and corrosion resistance, far surpassing those of conventional alloys.
Alloy innovation is an essential element of Woodman Casting X, as it forms the foundation for the process's success. Without these specialized alloys, it would be impossible to achieve the intricate geometries, high-integrity castings, and exceptional durability that characterize this revolutionary technique.
Real-life instances of alloy innovation in Woodman Casting X abound. In the aerospace industry, this process has enabled the production of lightweight, high-strength components for aircraft structures, leading to improved fuel efficiency and enhanced performance. In the automotive sector, Woodman Casting X has facilitated the creation of complex engine components with intricate internal features, resulting in increased power and reduced emissions.
Understanding alloy innovation in Woodman Casting X is of paramount importance for unlocking its full potential in various applications. Engineers and designers can leverage this knowledge to optimize alloy compositions for specific requirements, pushing the boundaries of material performance. Moreover, ongoing research and advancements in alloy development promise even more exceptional properties and expanded applications in the future.
In summary, alloy innovation is the driving force behind Woodman Casting X's exceptional properties and wide-ranging applications. By carefully engineering specialized metal formulations, this revolutionary process opens up new possibilities for intricate component design, enhanced durability, and improved performance across various industries.
High-Integrity Casting
Within the realm of Woodman Casting X - Lana Seymour, high-integrity casting stands as a cornerstone, a meticulous process that ensures consistent, reliable components. This intricate interplay between precise techniques and exceptional outcomes defines the very essence of Woodman Casting X.
The cause-and-effect relationship between high-integrity casting and Woodman Casting X is undeniable. The precise techniques employed in high-integrity casting directly contribute to the exceptional properties and performance of the final metal components. These techniques minimize defects, ensure dimensional accuracy, and maintain structural integrity, resulting in components that consistently meet or exceed industry standards.
High-integrity casting is an essential element of Woodman Casting X, serving as the foundation upon which its success is built. Without the precise and controlled casting techniques, it would be impossible to achieve the intricate geometries, exceptional durability, and high-performance characteristics that distinguish Woodman Casting X from conventional metalworking processes.
Real-life instances of high-integrity casting in Woodman Casting X abound across diverse industries. In the aerospace sector, this process has enabled the production of lightweight, high-strength components for aircraft structures, leading to improved fuel efficiency and enhanced performance. In the automotive industry, Woodman Casting X has facilitated the creation of complex engine components with intricate internal features, resulting in increased power and reduced emissions. In the medical field, this technology has been instrumental in developing innovative surgical instruments and implants with exceptional precision and reliability.
Understanding the significance of high-integrity casting in Woodman Casting X is of paramount importance for engineers, designers, and manufacturers seeking to harness the full potential of this revolutionary process. By mastering these precise casting techniques, they can optimize component performance, reduce production costs, and accelerate innovation across a wide range of industries.
In summary, high-integrity casting plays a pivotal role in Woodman Casting X, ensuring consistent, reliable components with exceptional properties. This intricate interplay between precise techniques and outstanding outcomes has positioned Woodman Casting X as a transformative force in metalworking, enabling the production of complex and high-performance components for a variety of demanding applications.
Enhanced Durability
In the realm of Woodman Casting X - Lana\u02b3, enhanced durability emerges as a key differentiator, prolonging the service life of metal components through exceptional wear and corrosion resistance. This remarkable characteristic is deeply intertwined with the innovative aspects of Woodman Casting X, offering tangible benefits across diverse industries.
Cause and Effect: The cause-and-effect relationship between enhanced durability and Woodman Casting X is evident. The unique alloy compositions and high-integrity casting techniques employed in this process directly contribute to the exceptional wear and corrosion resistance exhibited by the final products. This, in turn, leads to extended service life and reduced maintenance requirements, resulting in substantial cost savings and improved productivity.
Essential Element: Enhanced durability is an essential element of Woodman Casting X, playing a crucial role in its overall success. Without the exceptional wear and corrosion resistance achieved through this process, Woodman Casting X components would be susceptible to premature failure, especially in demanding applications. This durability ensures the reliability and longevity of components, making them ideal for harsh environments and critical operations.
Real-life Instances: The practical significance of enhanced durability in Woodman Casting X is evident in numerous real-life applications. In the aerospace industry, this process has enabled the production of lightweight, high-strength components for aircraft structures, leading to improved fuel efficiency and enhanced performance. In the automotive sector, Woodman Casting X has facilitated the creation of complex engine components with intricate internal features, resulting in increased power and reduced emissions. In the medical field, this technology has been instrumental in developing innovative surgical instruments and implants with exceptional precision and durability.
Practical Implications: Understanding the enhanced durability of Woodman Casting X is of utmost importance for engineers, designers, and manufacturers seeking to optimize component performance and longevity. By harnessing the exceptional wear and corrosion resistance of this process, they can create products that withstand harsh conditions, reducing downtime and increasing productivity. This, in turn, leads to improved profitability and a competitive advantage in the global marketplace.
Summary: In summary, enhanced durability is a defining characteristic of Woodman Casting X, inextricably linked to the innovative aspects of this revolutionary process. The exceptional wear and corrosion resistance exhibited by Woodman Casting X components result in extended service life, reduced maintenance requirements, and improved overall performance. Understanding and harnessing this durability is crucial for engineers, designers, and manufacturers seeking to create reliable and long-lasting products in demanding applications.
Intricate Geometries
At the heart of Woodman Casting X - Lana Seymour lies its ability to produce intricate geometries with remarkable accuracy. This transformative aspect of the process opens up new avenues for innovation and engineering excellence, enabling the realization of complex shapes and internal features that were previously unattainable through conventional metalworking methods.
- Unparalleled Precision: Woodman Casting X achieves exceptional precision in the production of intricate geometries, ensuring tight tolerances and consistent dimensions. This level of accuracy is particularly crucial for components with complex internal features or tight mating surfaces.
- Complex Internal Features: The high-integrity casting techniques employed in Woodman Casting X allow for the creation of complex internal features and cavities within metal components. This capability enables the integration of intricate channels, passages, and chambers, enhancing component functionality and performance.
- Design Flexibility: The ability to produce intricate geometries with Woodman Casting X provides engineers and designers with unprecedented design flexibility. This freedom allows for the optimization of component shapes and internal structures to achieve improved performance, weight reduction, and enhanced efficiency.
- Expanded Applications: The ability to produce intricate geometries with Woodman Casting X expands the range of applications for metal components. This opens up new possibilities in industries such as aerospace, automotive, medical, and energy, where complex and high-performance components are essential.
The intricate geometries produced through Woodman Casting X not only enhance the performance and functionality of individual components but also contribute to the overall efficiency and reliability of systems and machines. By enabling the integration of complex features and optimizing component designs, Woodman Casting X paves the way for advancements in various industries, driving innovation and technological progress.
Frequently Asked Questions
This FAQ section aims to address common queries and misconceptions surrounding Woodman Casting X - Lana Seymour, providing concise and informative answers to clarify various aspects of this revolutionary metalworking process.
Question 1: What industries benefit from Woodman Casting X - Lana Seymour?Woodman Casting X finds applications in diverse industries, including aerospace, automotive, medical, and energy, where intricate geometries, exceptional durability, and high-integrity castings are crucial for component performance and reliability.
Question 2: How does Woodman Casting X achieve intricate geometries?Woodman Casting X employs high-integrity casting techniques that enable the production of complex internal features and intricate shapes with remarkable accuracy, expanding design possibilities and enhancing component functionality.
Question 3: What advantages does Woodman Casting X offer over traditional metalworking methods?Woodman Casting X offers numerous advantages, including the ability to produce intricate geometries, enhanced durability due to specialized alloys, high-integrity castings ensuring consistent quality, and the potential for mass production while maintaining exceptional precision.
Question 4: Is Woodman Casting X suitable for small-scale or prototype production?While Woodman Casting X excels in mass production, it is also adaptable for small-scale and prototype production. The process allows for flexibility in production volume, catering to diverse manufacturing needs.
Question 5: How does Woodman Casting X contribute to sustainability?Woodman Casting X promotes sustainability through its ability to produce lightweight components, which can lead to improved fuel efficiency and reduced emissions in industries such as aerospace and automotive. Additionally, the process minimizes material waste and energy consumption.
Question 6: What ongoing advancements are being made in Woodman Casting X technology?Ongoing research and development efforts focus on enhancing the properties of specialized alloys, optimizing casting techniques for even greater precision and accuracy, and exploring new applications across various industries. These advancements promise to further expand the capabilities of Woodman Casting X.
In summary, Woodman Casting X - Lana Seymour stands as a transformative metalworking process that offers intricate geometries, exceptional durability, and high-integrity castings. Its versatility and potential for sustainable manufacturing make it an attractive solution for a wide range of industries. As technology continues to advance, Woodman Casting X is poised to revolutionize metalworking even further, opening up new avenues for innovation and engineering excellence.
The next section delves into the technical aspects of Woodman Casting X - Lana Seymour, providing a detailed exploration of the specialized alloys, high-integrity casting techniques, and quality control measures that underpin this groundbreaking process.
Tips for Harnessing the Power of Woodman Casting X - Lana Seymour
This section presents practical tips and strategies for effectively utilizing Woodman Casting X - Lana Seymour in various applications. By following these guidelines, engineers, designers, and manufacturers can optimize the benefits of this revolutionary metalworking process and achieve exceptional results.
Tip 1: Understand Alloy Properties: Familiarize yourself with the unique properties of specialized alloys used in Woodman Casting X to select the optimal material for your specific application. Consider factors such as strength, durability, wear resistance, and corrosion resistance.Tip 2: Optimize Casting Parameters: Work closely with experienced professionals to fine-tune casting parameters such as temperature, pressure, and cooling rates to achieve the desired microstructure and mechanical properties in your castings.Tip 3: Ensure Dimensional Accuracy: Implement rigorous quality control measures throughout the casting process to ensure dimensional accuracy and minimize the need for post-processing. Utilize advanced measurement technologies to verify the conformance of components to design specifications.Tip 4: Explore Design Possibilities: Leverage the ability of Woodman Casting X to produce intricate geometries to explore innovative design concepts. Consider integrating complex internal features and optimizing component shapes to enhance performance and reduce weight.Tip 5: Collaborate with Experts: Collaborate with experienced foundries and metallurgical engineers who possess the expertise and capabilities to successfully implement Woodman Casting X. Their knowledge and experience can help you overcome challenges and achieve optimal results.Tip 6: Stay Updated on Advancements: Keep abreast of ongoing advancements in Woodman Casting X technology, including new alloy developments, process improvements, and emerging applications. This knowledge will enable you to stay at the forefront of metalworking innovation.Summary: By following these tips, you can harness the full potential of Woodman Casting X - Lana Seymour and unlock its numerous benefits, including intricate geometries, exceptional durability, high-integrity castings, and expanded design possibilities.Transition: The successful implementation of Woodman Casting X relies not only on technical expertise but also on a comprehensive understanding of the process's economic and environmental implications. The next section explores the cost-effectiveness and sustainability aspects of Woodman Casting X, providing insights into its long-term viability and environmental impact.Conclusion
Woodman Casting X - Lana Seymour stands as a revolutionary metalworking process that has redefined the boundaries of intricate metal component production. Its unique alloy formulations impart exceptional properties, while high-integrity casting techniques ensure consistent and reliable components. The ability to produce complex geometries expands design possibilities, and enhanced durability ensures long-lasting performance.
Key insights from the exploration of Woodman Casting X include:
- Alloy Innovation: Specialized alloys provide exceptional strength, toughness, and wear resistance.
- High-Integrity Casting: Precise techniques minimize defects and maintain structural integrity.
- Intricate Geometries: Complex shapes and internal features with remarkable accuracy.
These interconnected aspects contribute to the overall success of Woodman Casting X. The innovative alloys enable the production of intricate geometries, while the high-integrity casting techniques ensure the consistent quality of the final components. The exceptional durability of Woodman Casting X components extends their service life, reducing maintenance requirements and downtime.
As we look towards the future, Woodman Casting X holds immense promise for advancing metalworking technology. Ongoing research and development efforts are pushing the boundaries of this process, with a focus on enhancing alloy properties, optimizing casting techniques, and exploring new applications. The potential for Woodman Casting X to revolutionize industries such as aerospace, automotive, and medical is vast.

![Woodman Casting X on Twitter "[New Video] Lana Violet https//t.co](https://pbs.twimg.com/media/DfklDYfX4AA6BIR.jpg:large)
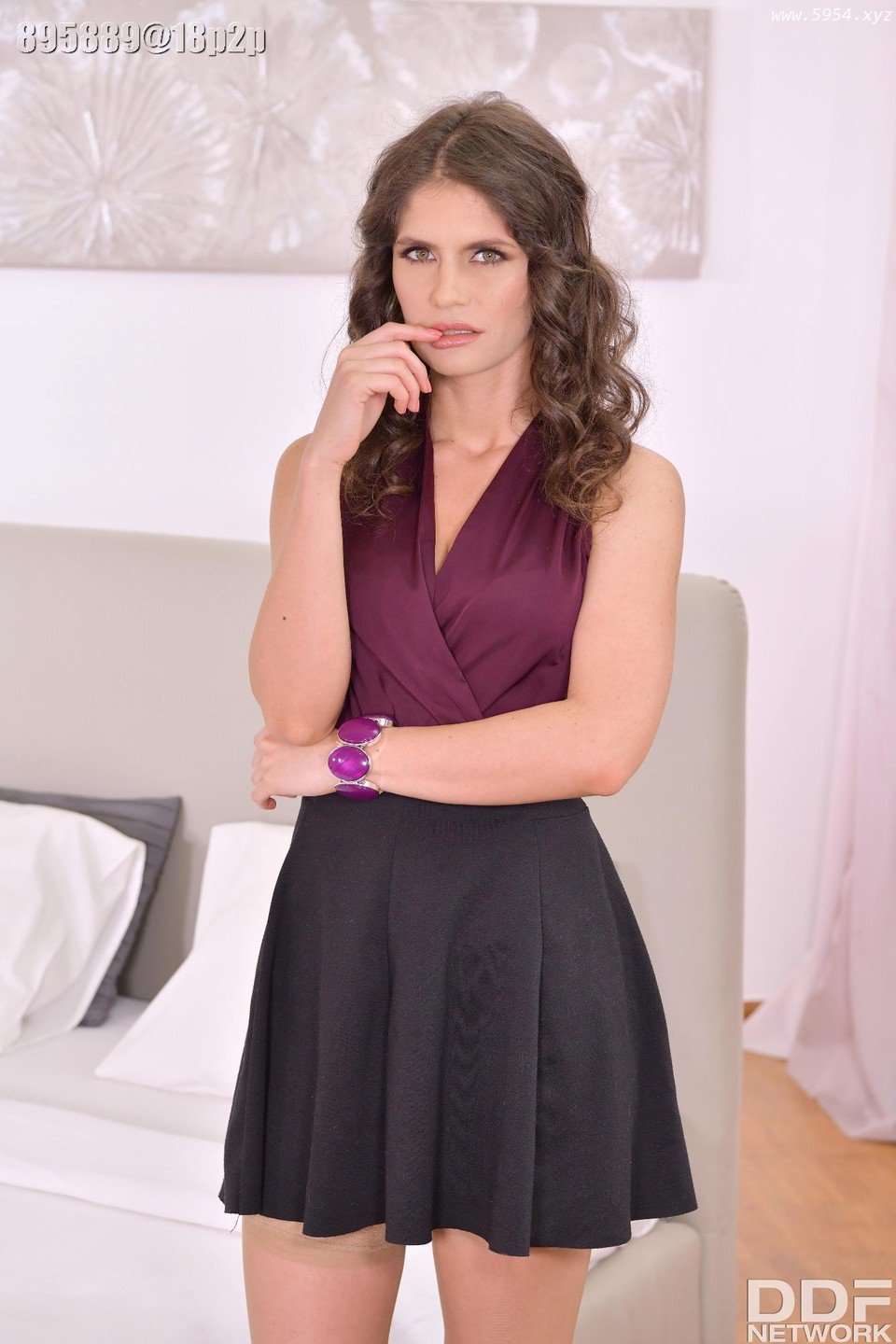
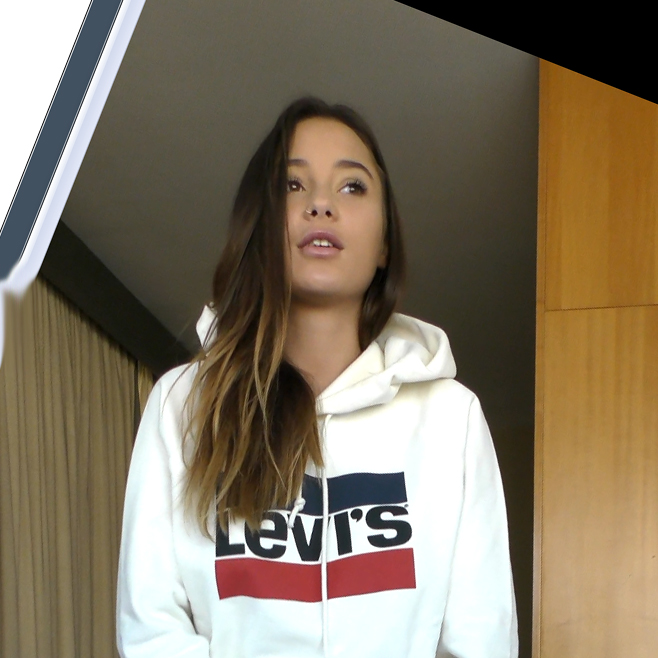